Key Drivers: Efficiency & Profitability
Modular and prefabrication construction is gaining traction as an efficient method for building construction projects. Driven by factors such as skilled labor shortages and the need for better project predictability, the market is seeing continual adoption of some level of prefabricated solutions.
Prefab vs. Modular Markets: What’s the Difference?
It is important to understand the differences between prefabrication and modular construction. Prefab construction involves the manufacturing of a building or building component in a factory before final assembly at the construction site.
Modular construction, on the other hand, refers to structures built or organized in self-contained units, like building blocks, with a significant portion completed in the factory prior to delivery. A general rule of thumb suggests that a modular construction would consist of at least 70% of the work being completed in the factory.
All modular buildings are considered prefabs, but not all prefabs are modular.
The Commercial Modular Market
The Modular Building Institute defines two types of commercial modular buildings – relocatable and permanent. Relocatable buildings are partially or completely assembled buildings designed and constructed to be reused multiple times and transported to different building sites. Relocatable modular building are available in fleets and offered either for sale or leasing. Applications for relocatable modular buildings include use as temporary housing for field office, field personnel in construction, oil/gas, and disaster relief.
Permanent modular construction (PMC) is a delivery method utilizing offsite, lean manufacturing techniques to prefabricate single and multistory building solutions in deliverable module sections. PMC units can be constructed of wood, steel, or concrete; are integrated into site-built projects, or as stand-alone units; and can be delivered with mechanical, electrical, plumbing, fixtures, and interior finishes.
The Modular Building Institute recently published the 2023 Permanent Modular Construction Report that offered a financial analysis of the market from 2015 through 2022. It shows a consistent adoption of a permanent modular construction approach culminating with an estimated 6% market share for all U.S. commercial construction starts in 2022. And that figure does not reflect any prefabrication involvement.
For commercial construction, the initial growth in the PMC market is centered around the multi-family segment, likely due to the high need for replication of standardized multiple units that can be better controlled in a manufacturing site setting.
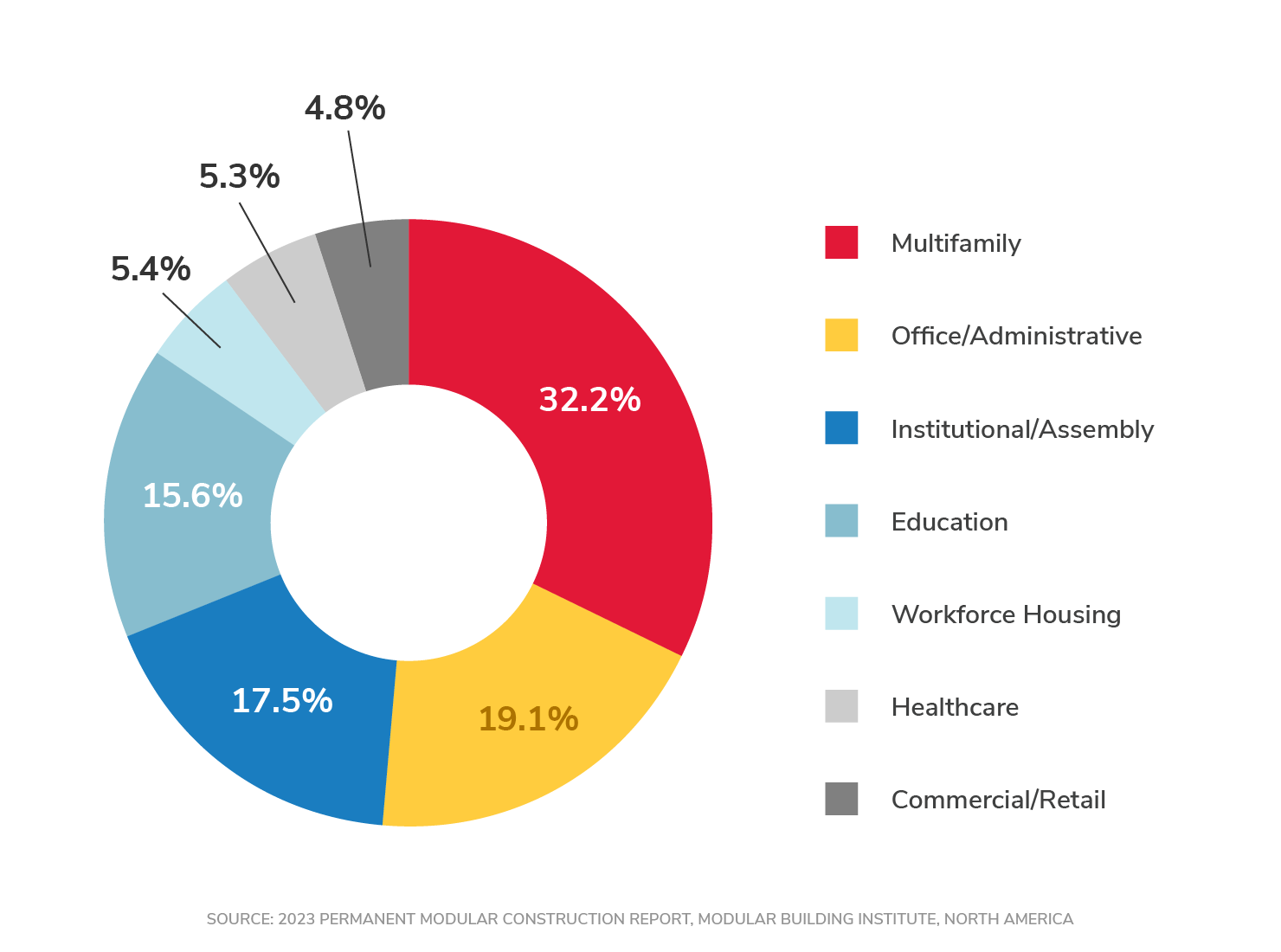
That same report shows healthcare facilities, hotels, motels, multifamily buildings, and college buildings/dormitories are the most likely building types to benefit from adopting this emerging methodology.
Market Influences and Modular Advantages
Several factors are driving the modular construction market, including a skilled labor shortage, increased project predictability, sustainability initiatives, and improved worker safety. Modular construction offers cost savings, shorter construction schedules, reduced waste, and better safety performance compared to traditional construction methods. Taken together, this drives greater profitability and efficiency on nearly any construction project.
Modular Construction Manufacturers
The Modular Building Institute estimates there are 255 modular construction manufacturers in the U.S., with 122 being members of Modular Building Institute (MBI). Manufacturers in this space are a combination of permanent modular construction and relocatable. While there are several players in this emerging, it is beginning to consolidate itself with manufacturers like BOXX Modular acquiring competitor Vanguard Building Systems, and VESTA Modular acquiring Commercial Mobile Systems. There are solid modular manufacturers present throughout the U.S.
Trends in Modular and Prefab Construction
Container-based structures and tiny homes are emerging trends in the modular construction market. Container-based structures save space and provide an industrial feel, making them suitable for both residential and commercial applications. Tiny homes, which according to Porch.com average 225 square feet and cost around $52,000, offer an alternative housing solution for those who value minimalism.
An example of an emerging prefabrication solution is Plungie Pools, who is working with builders to provide prefabricated concrete plunge pools as an easy and controllable add-on to a new home construction.
The Future of Modular Construction
Building and construction professionals of every kind – architects, designers, contractors, developers, installers, and building owners – are under constant pressure to deliver innovative building solutions on aggressive time schedules, and cost is always a factor.
Given these market pressures, the modular construction market is a dynamic and growing industry that offers numerous advantages over traditional construction methods. With an increasing number of modular manufacturers entering the market, and innovative trends emerging, the future of modular construction is set to make a significant impact on the construction industry as a whole.
Let’s talk.
Have a specific marketing challenge? Looking for a new agency?
We’d love to hear from you.